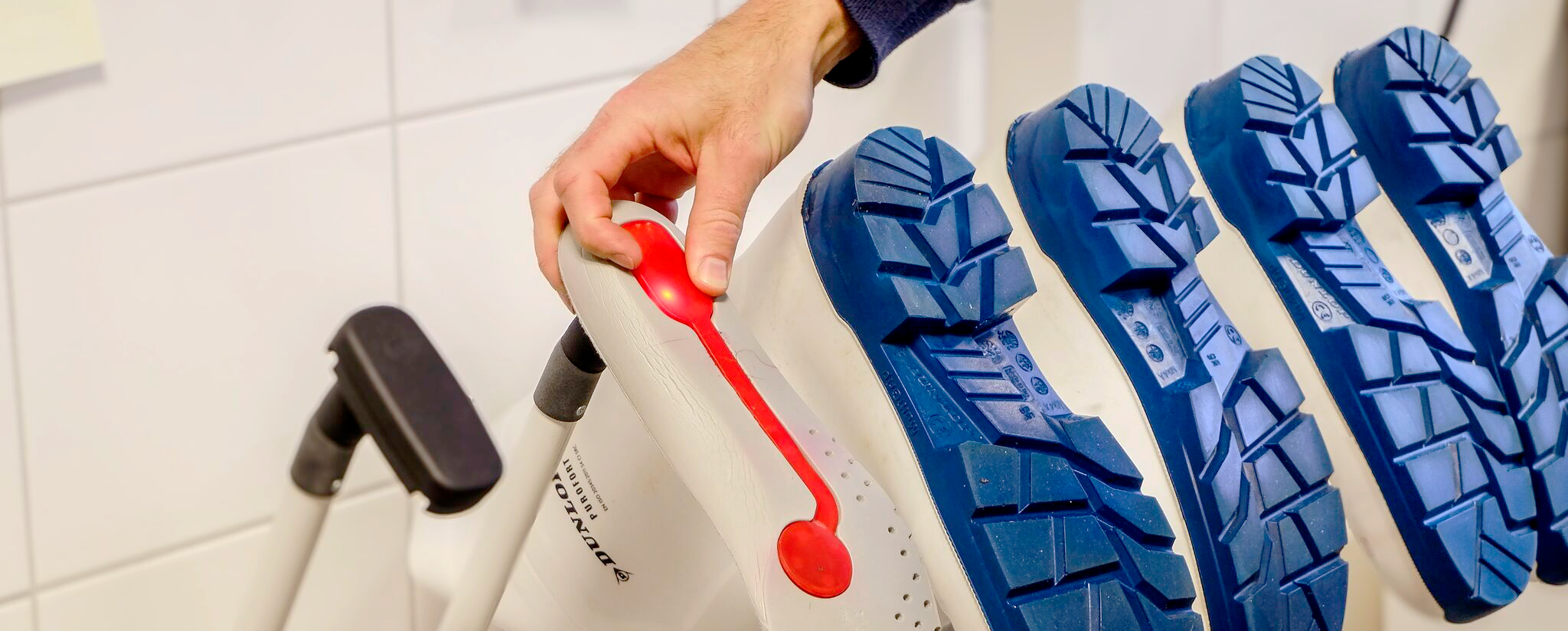
Dunlop Smart Insole
A modular smart insole that tracks real time data to prevent workplace injuries, whilst accomodating for varying foot sizes and minimising SKU’s.
Dunlop sought to add to their product lineup by introducing
an additional innovation: Smart Insoles, designed to empower businesses through comployee safety and health. By integrating pressure sensors and GPS tracking into a device that allows for real time monitoring of various
user metrics, preventing injuries and creating safe work environments. FLEX/design were tasked to design the 3D solution, the goal
was to create a modular solution that not only minimized financial strain for
Dunlop and consumers but also prioritized usability, ergonomics, SKU
optimization, repairability, and sustainability throughout the product
lifecycle.
Due to Non-Disclosure Agreements, all internal work cannot be shown.
Due to Non-Disclosure Agreements, all internal work cannot be shown.
Company
Client
Sector
FLEX/design
Dunlop
Footwear
Role
Responsibilities
Year
Designer
Ideation
Prototyping
Design for External Engineering
Material Testing
Manufacture Methods
Prototyping
Design for External Engineering
Material Testing
Manufacture Methods
2022
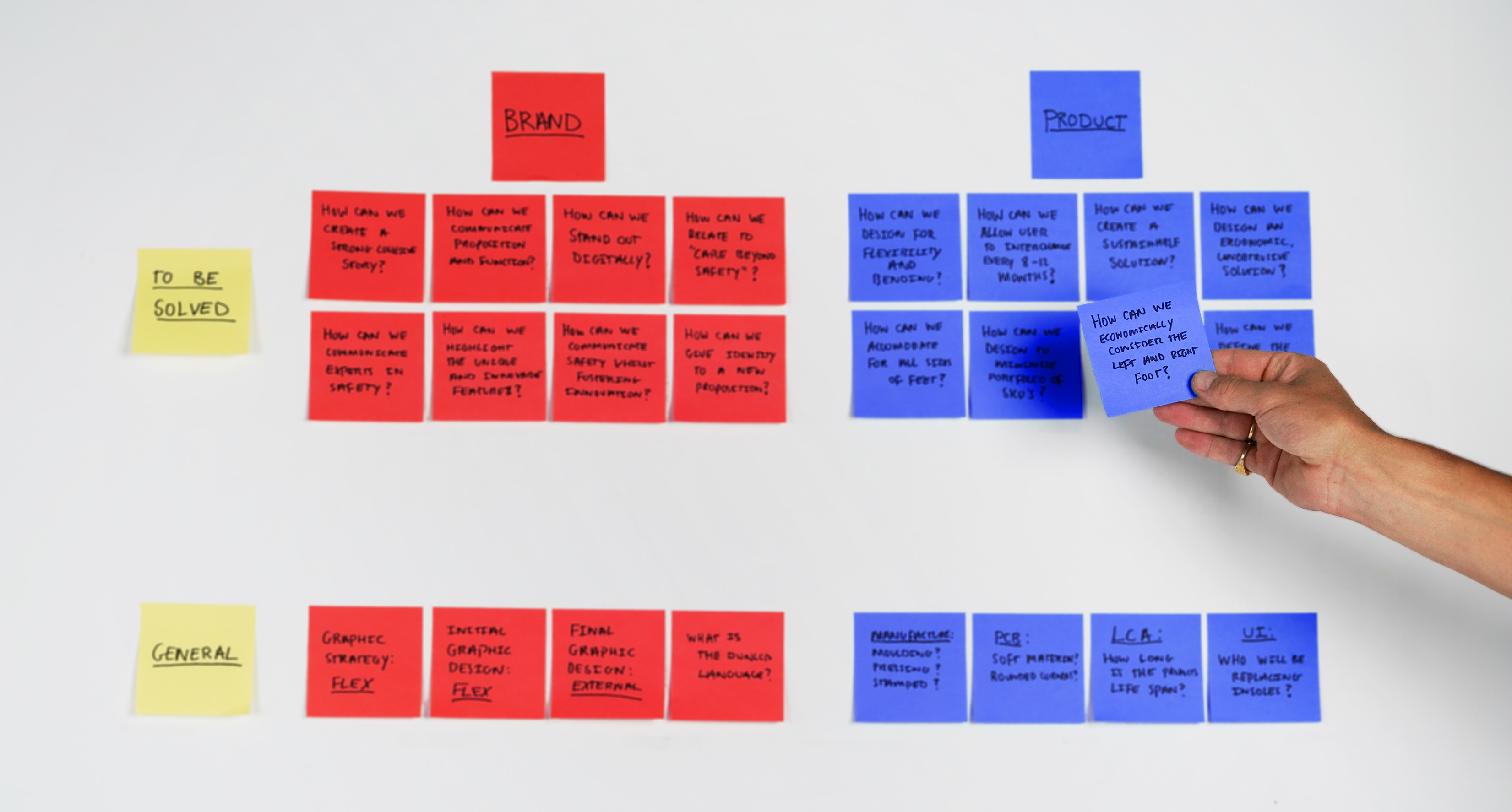
Creating a super secure subassembly.
Exploring parallel solutions for fixation methods that enable the temporary attachment of semi-integrated technology to an insole, creating a secure subassembly. This approach ensures stability while simplifying component replacement, supporting repair, electronic recyclability, and extending the product’s life cycle.


Sketch directions to spark discussion.
Each direction was freely explored in different variables. Securing methods, sustainability, life cycle, user interaction, SKUs, and brand communication were all carefully considered throughout the exploration process.



Reducing material hardness contrast.
Materials underwent iterative testing to evaluate their hardness, combining them against each other for analysis in contrast and how that consequently felt to the touch. These tests yielded valuable insights into how material contrasts impact ergonomics, usability, and functionality, informing the selection process for optimal performance and user experience.
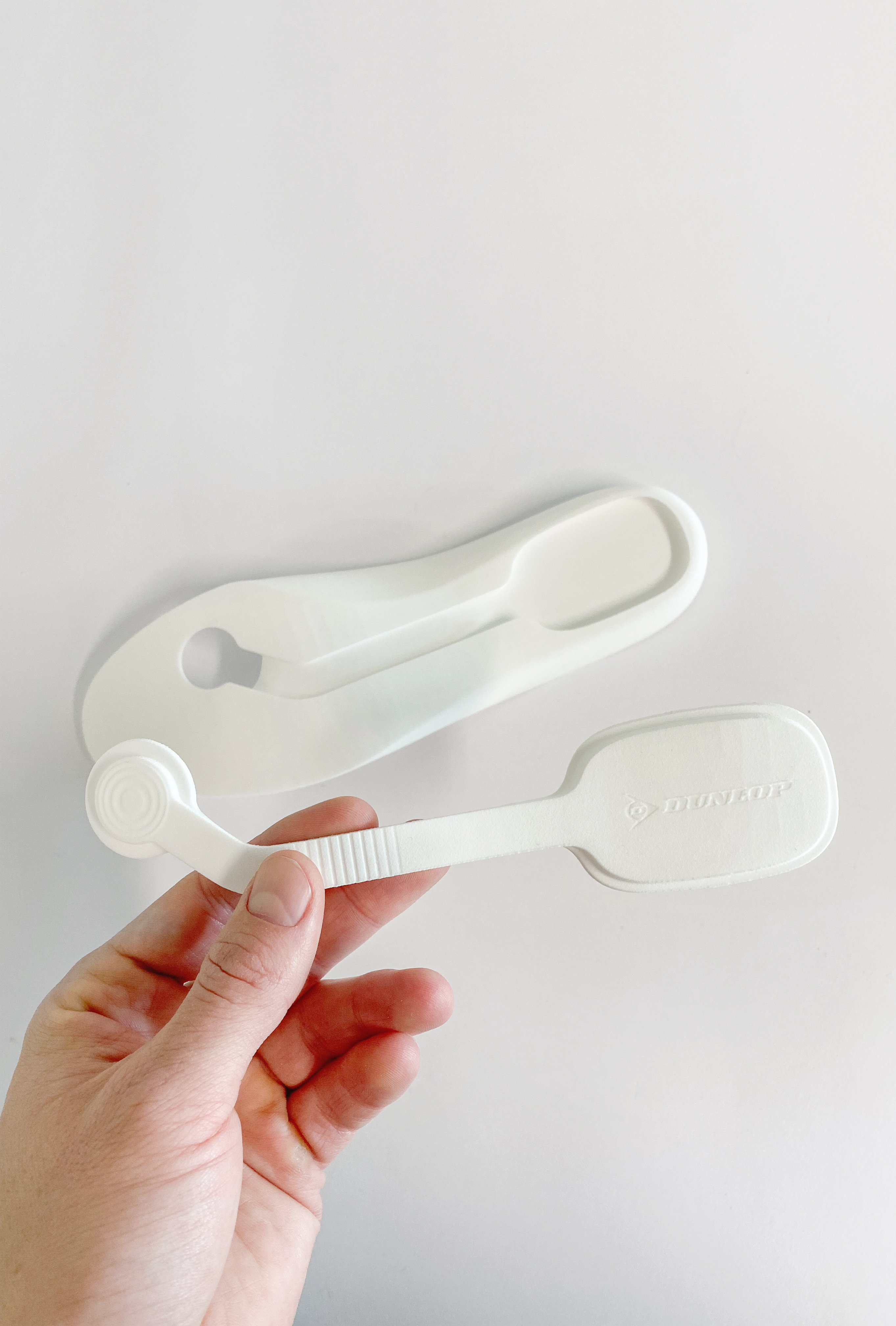
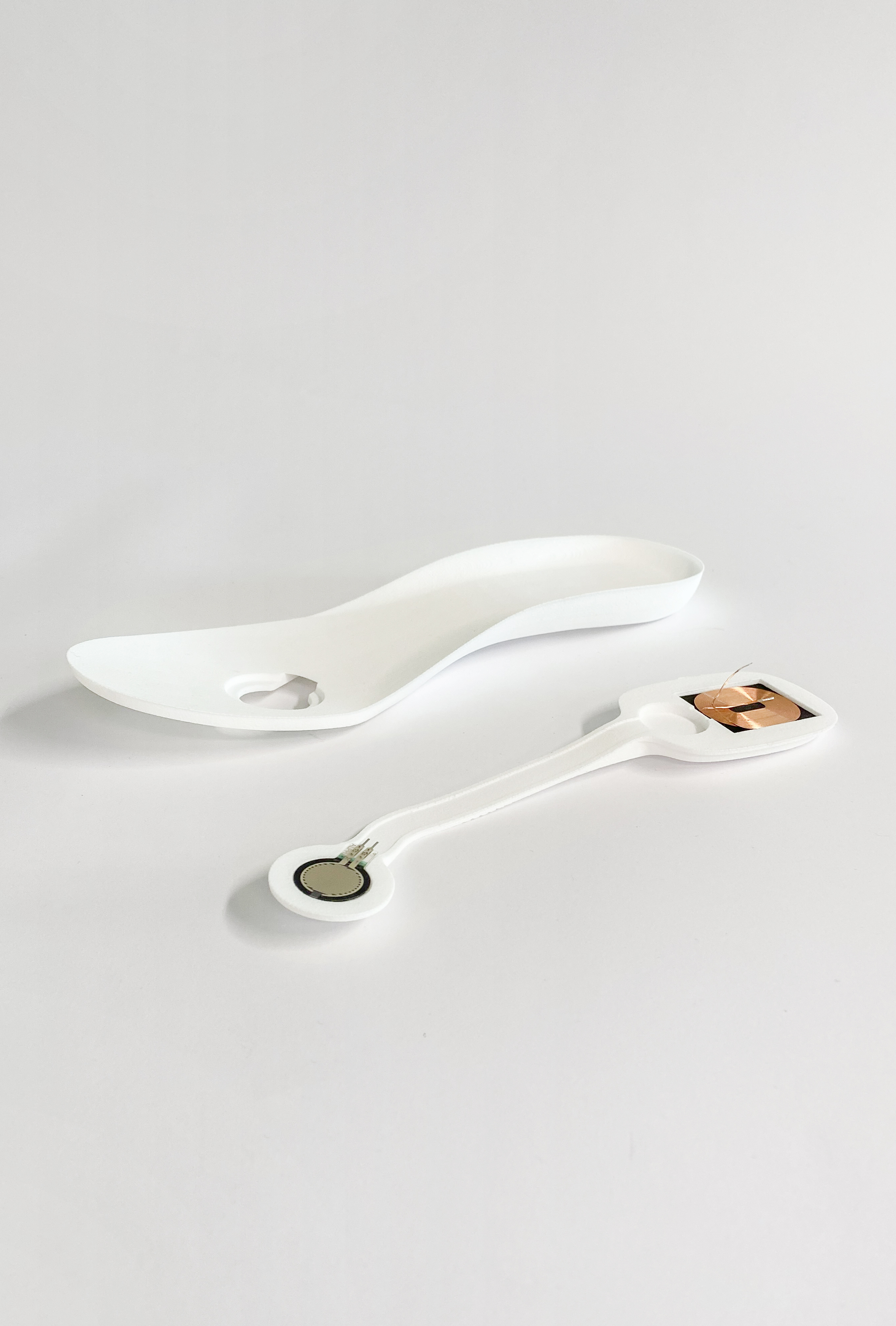


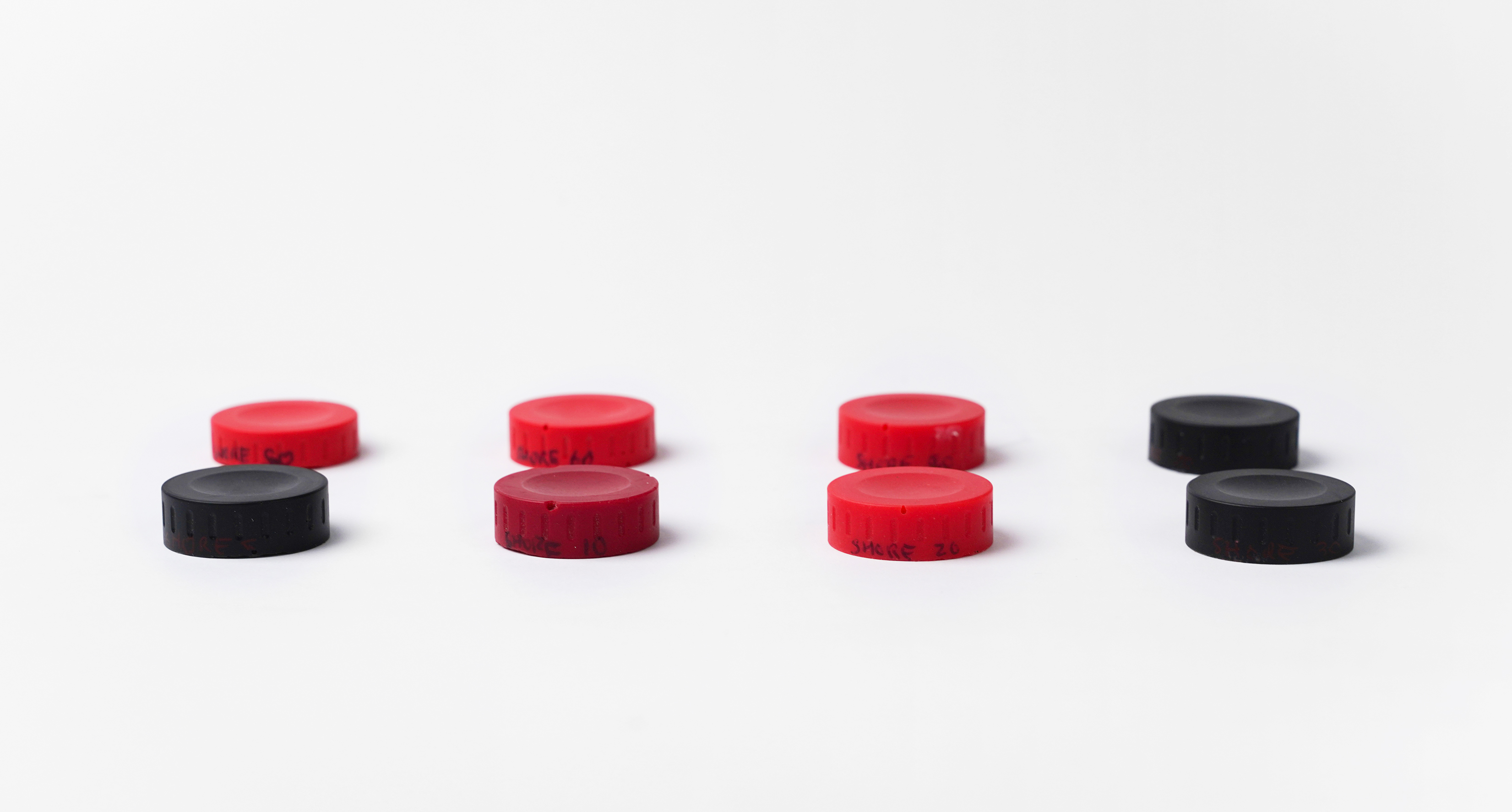
Utilising PU material properties.
Polyurethane has exceptional
formability and great flexibility, enabling the creation of intricate shapes
and accommodating undercuts in molds without compromising removal. This
feature allows for a snug fit around the Insert, ensuring a secure
subassembly before insertion into the boot.
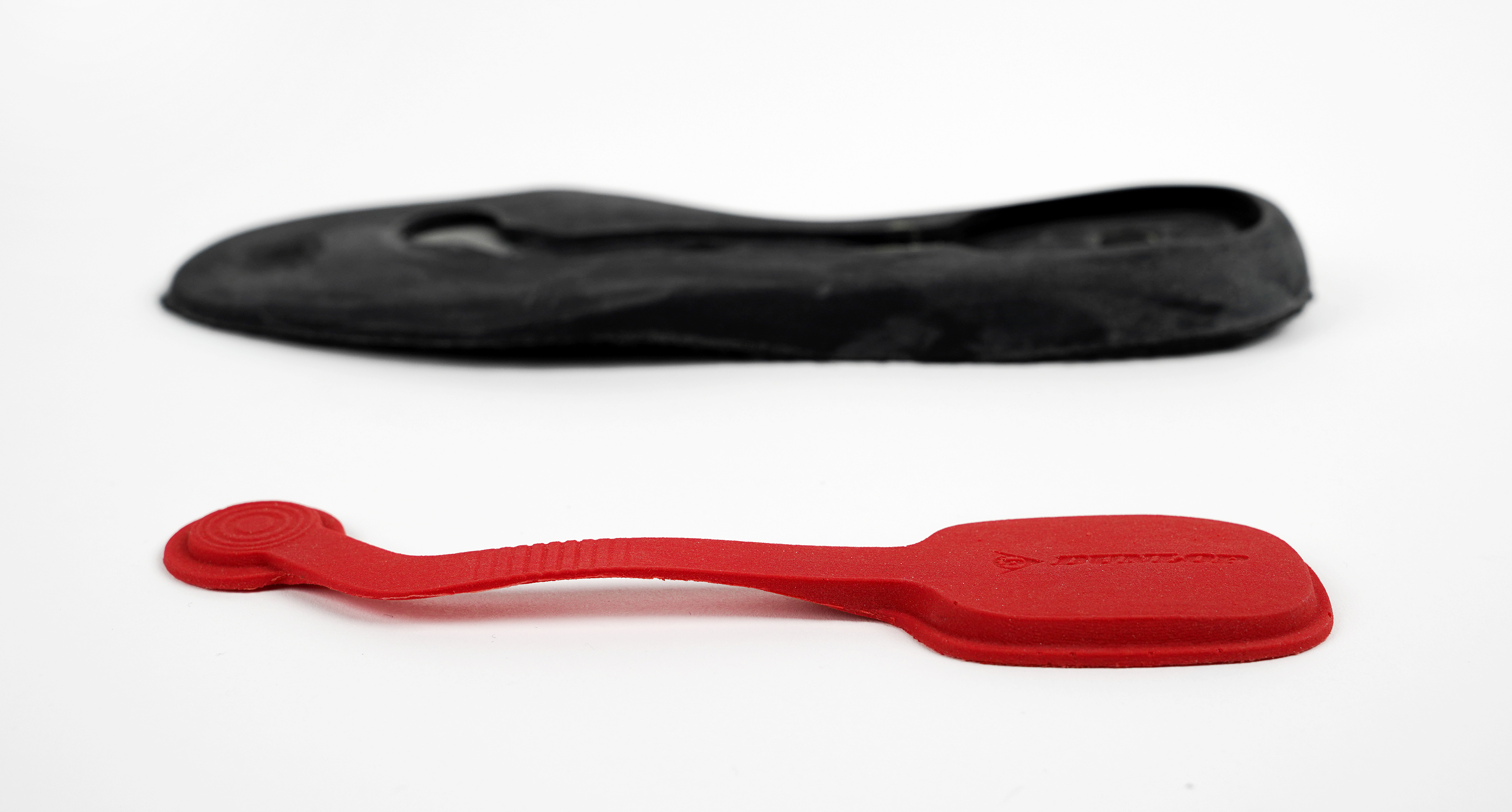
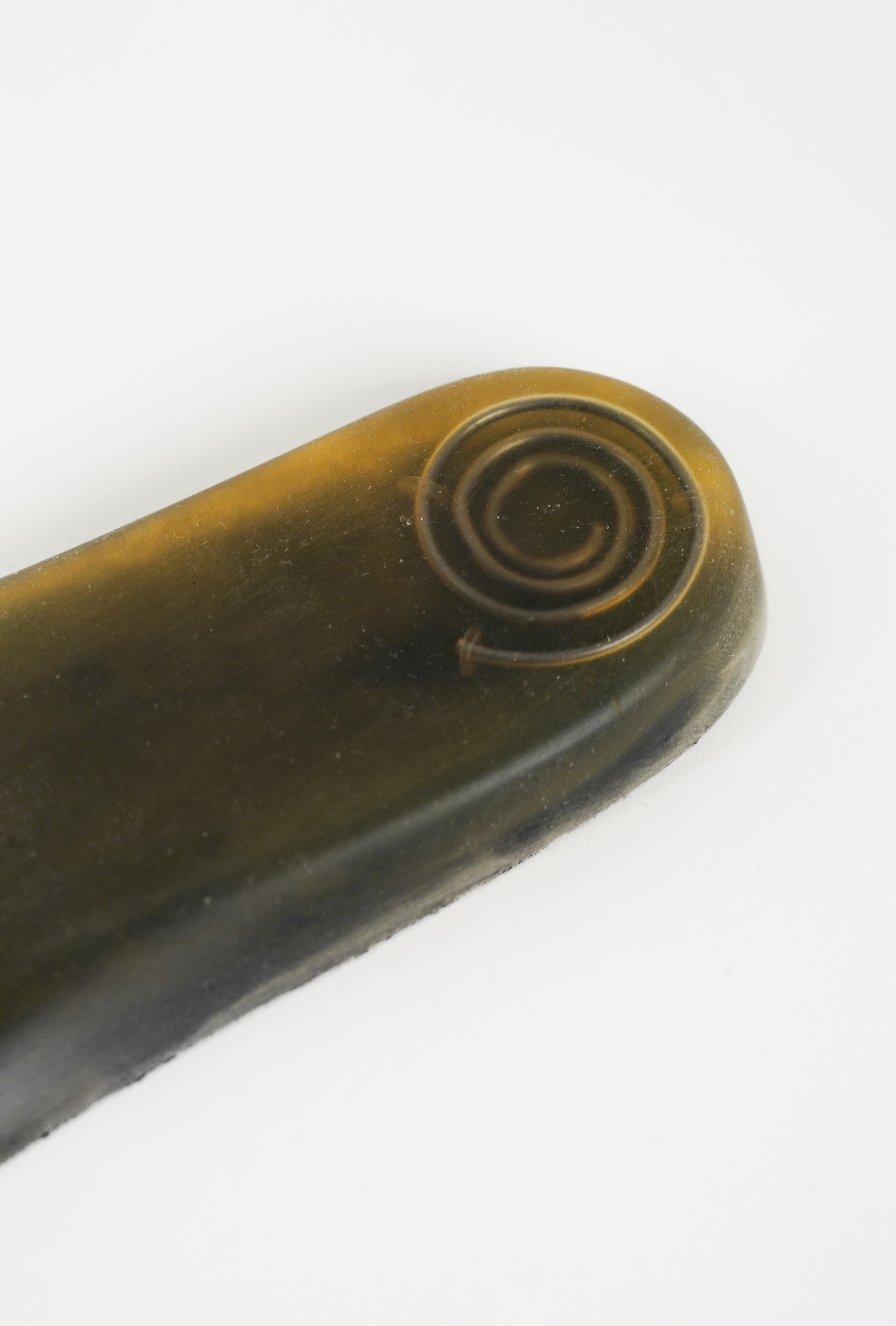
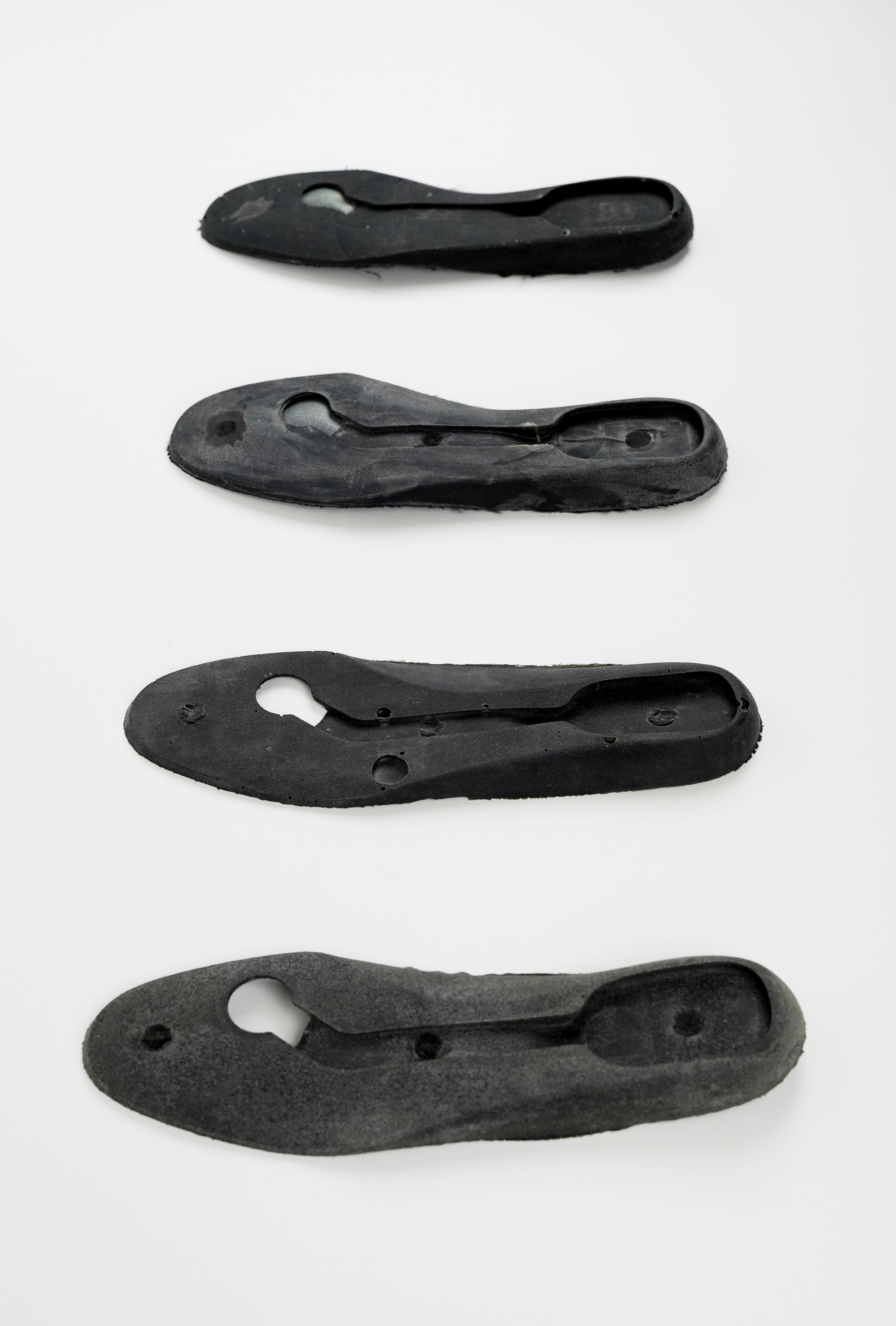

Standing out amongst the rest.
After multiple graphic iterations exploring various strategic directions, a final design was chosen. Utilising a white microfibre insole top, distinguishes itself from the rest of the dunlop portfolio, signaling the brand’s expansion into new, innovative segments.


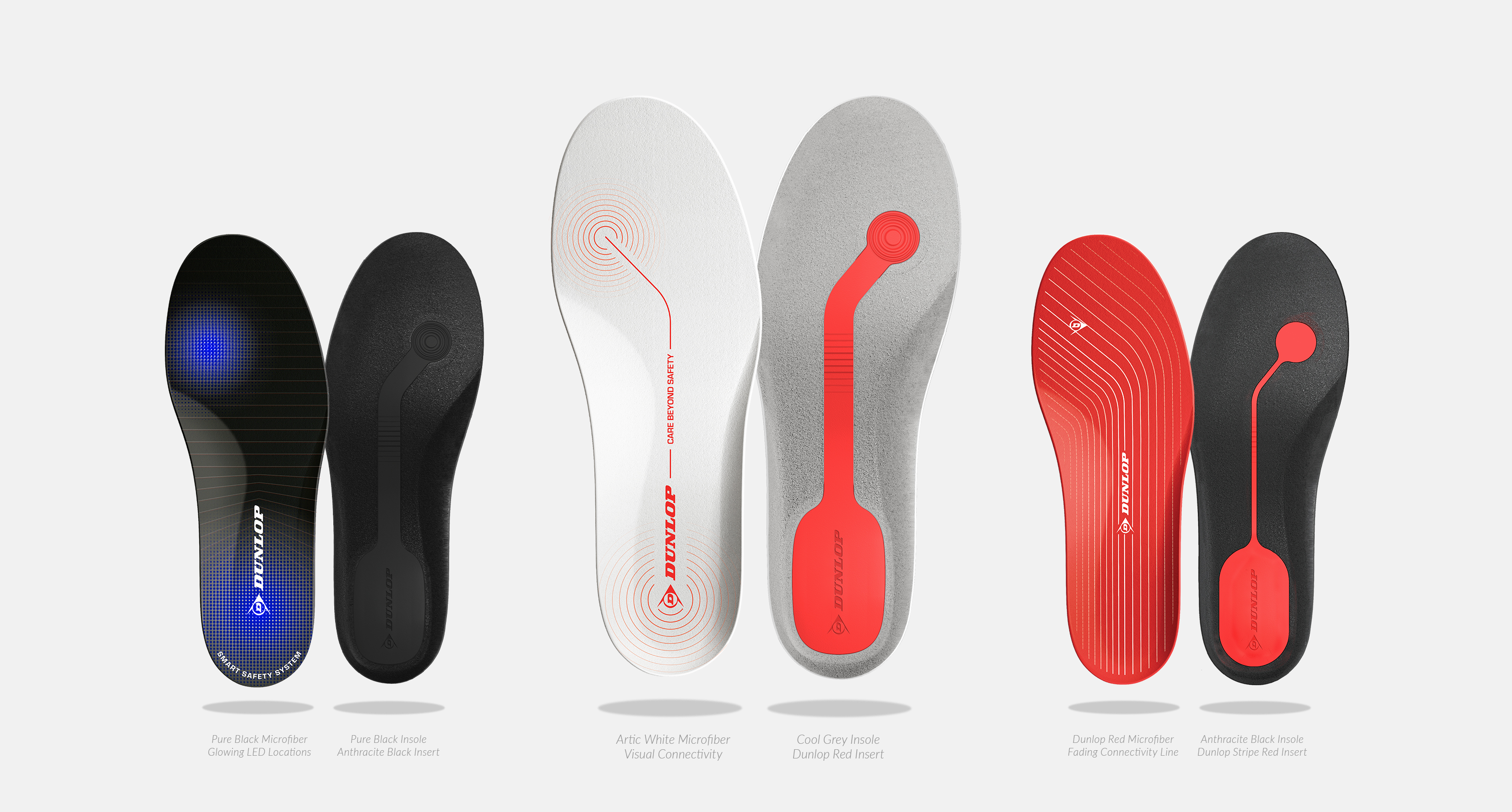
Utilising PU material properties.
Polyurethane has exceptional
formability and great flexibility, enabling the creation of intricate shapes
and accommodating undercuts in molds without compromising removal. This
feature allows for a snug fit around the Insert, ensuring a secure
subassembly before insertion into the boot.
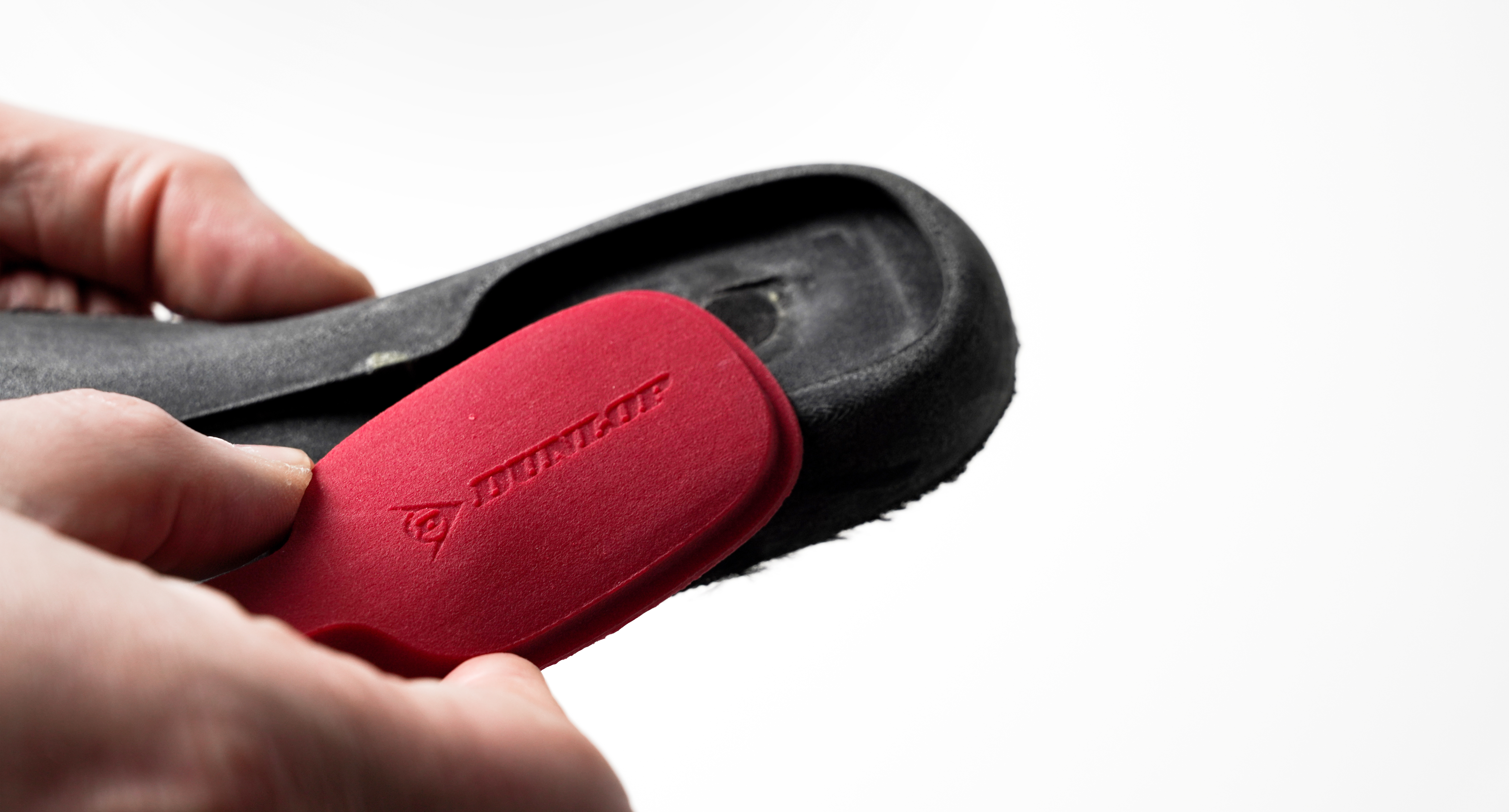
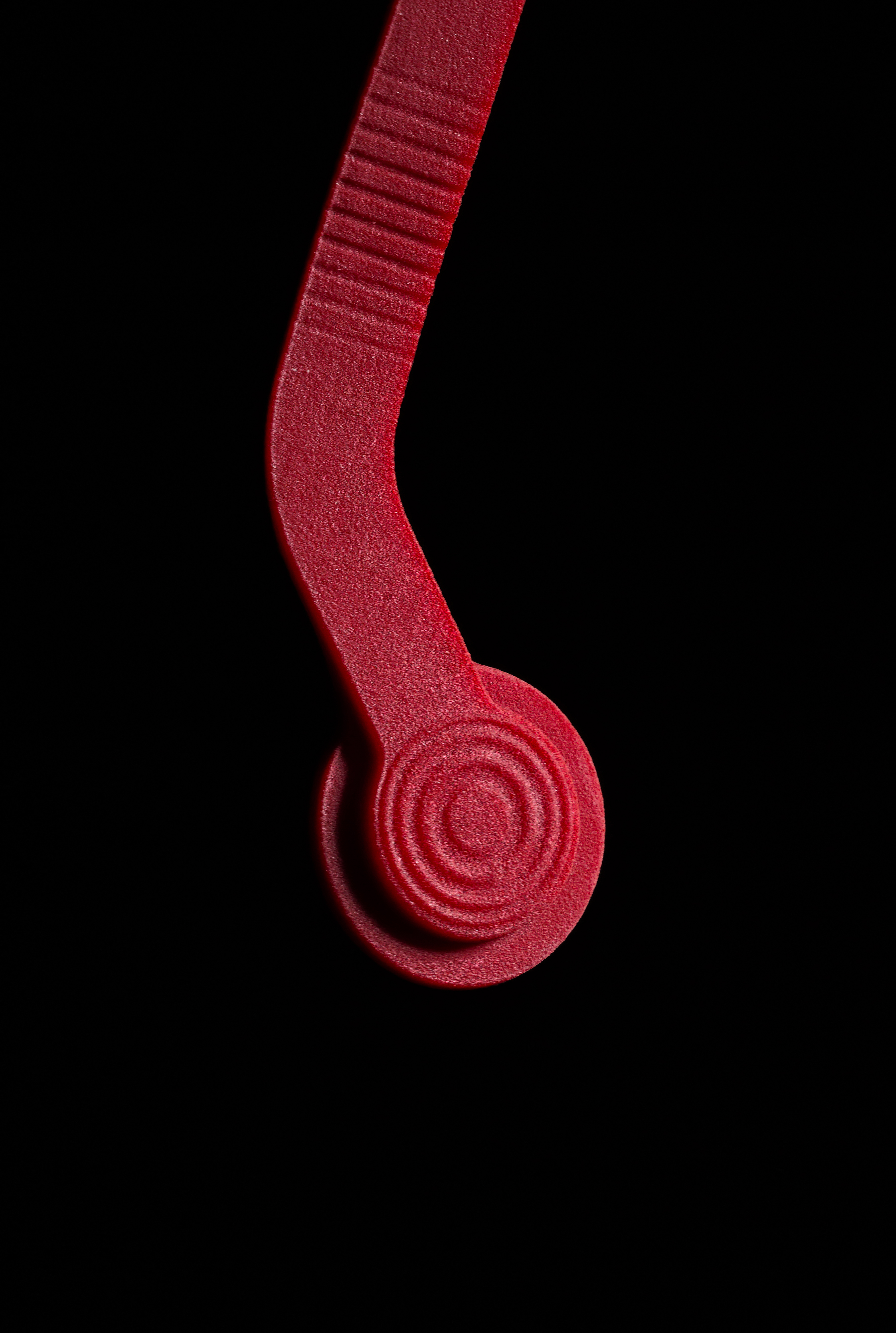
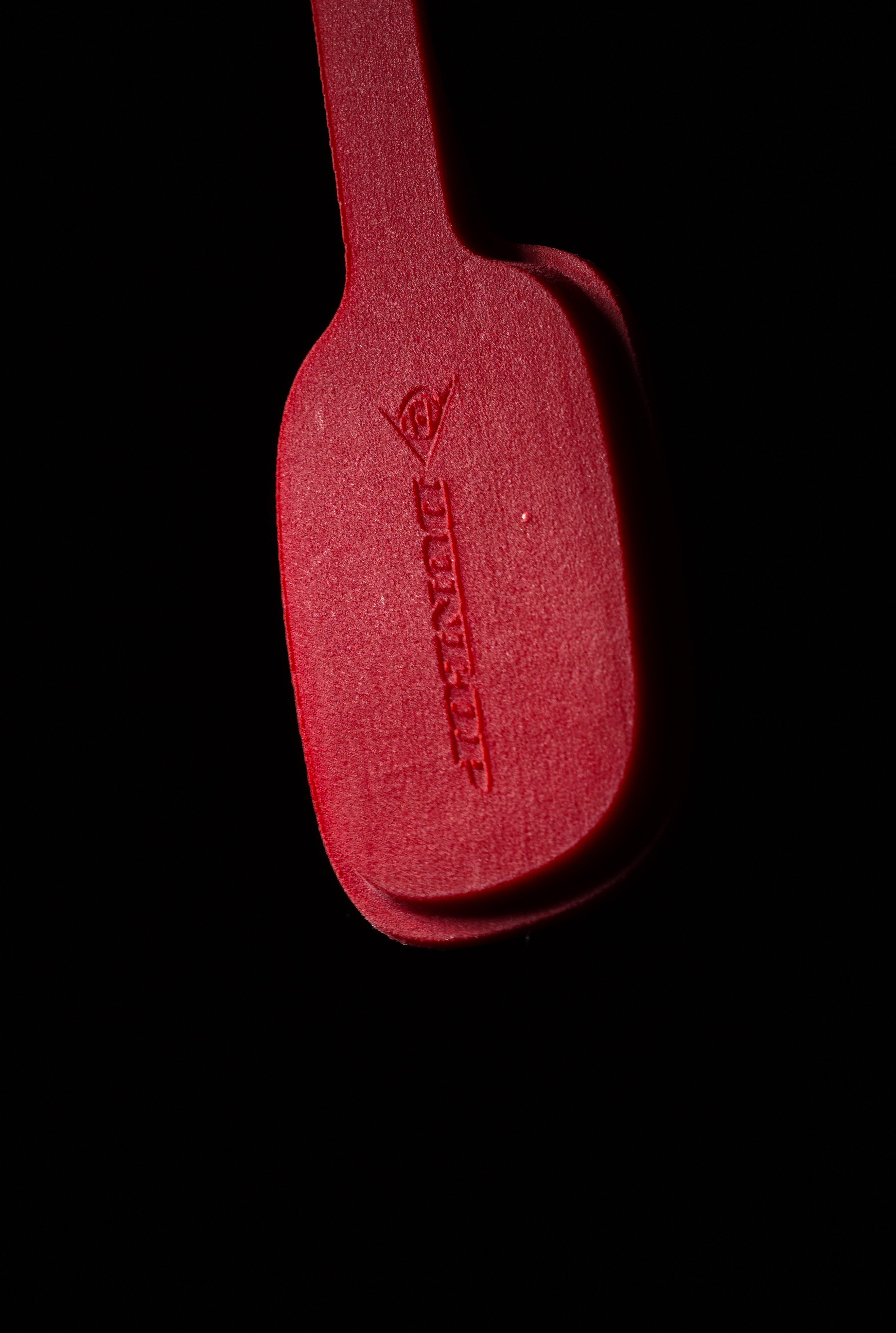
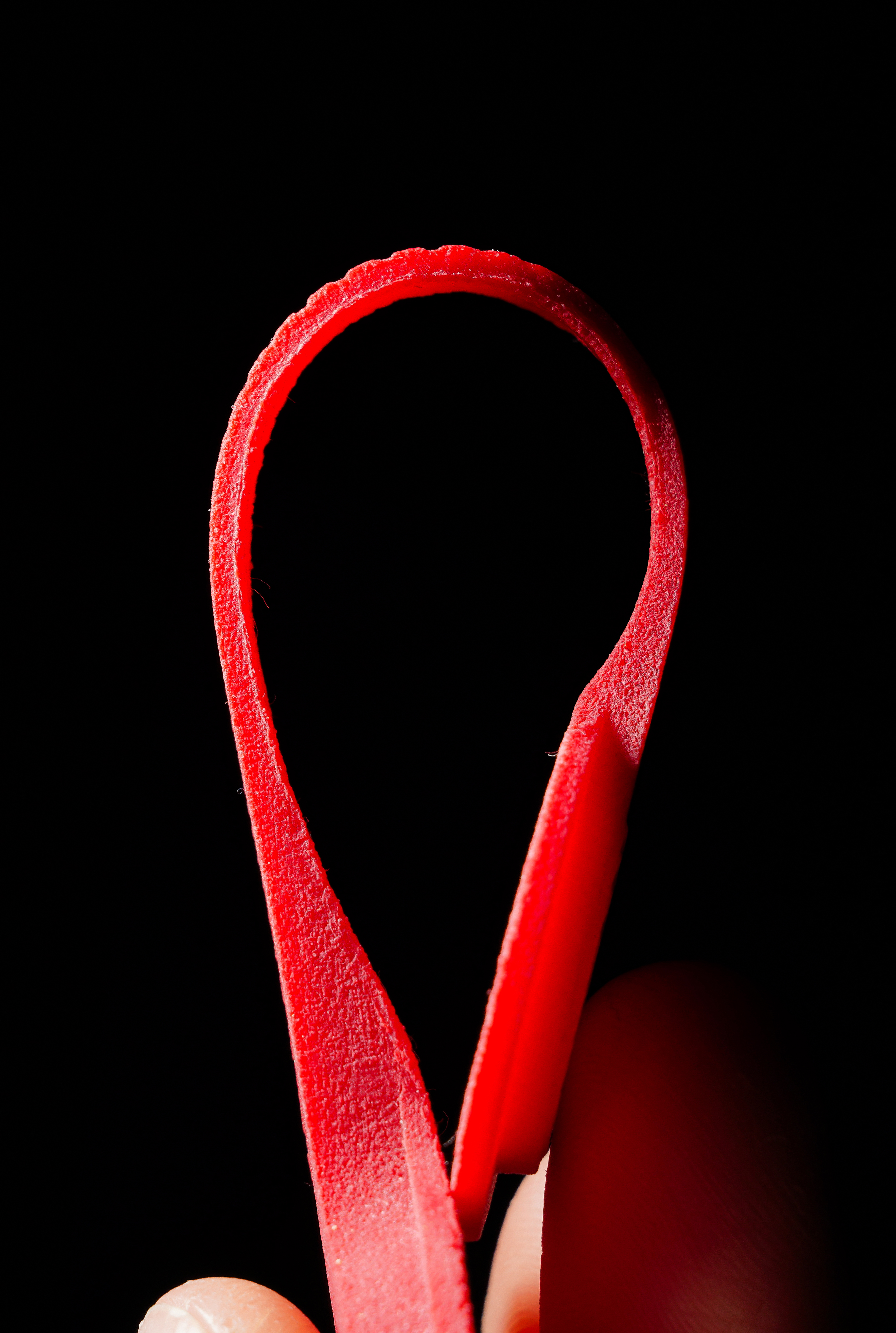
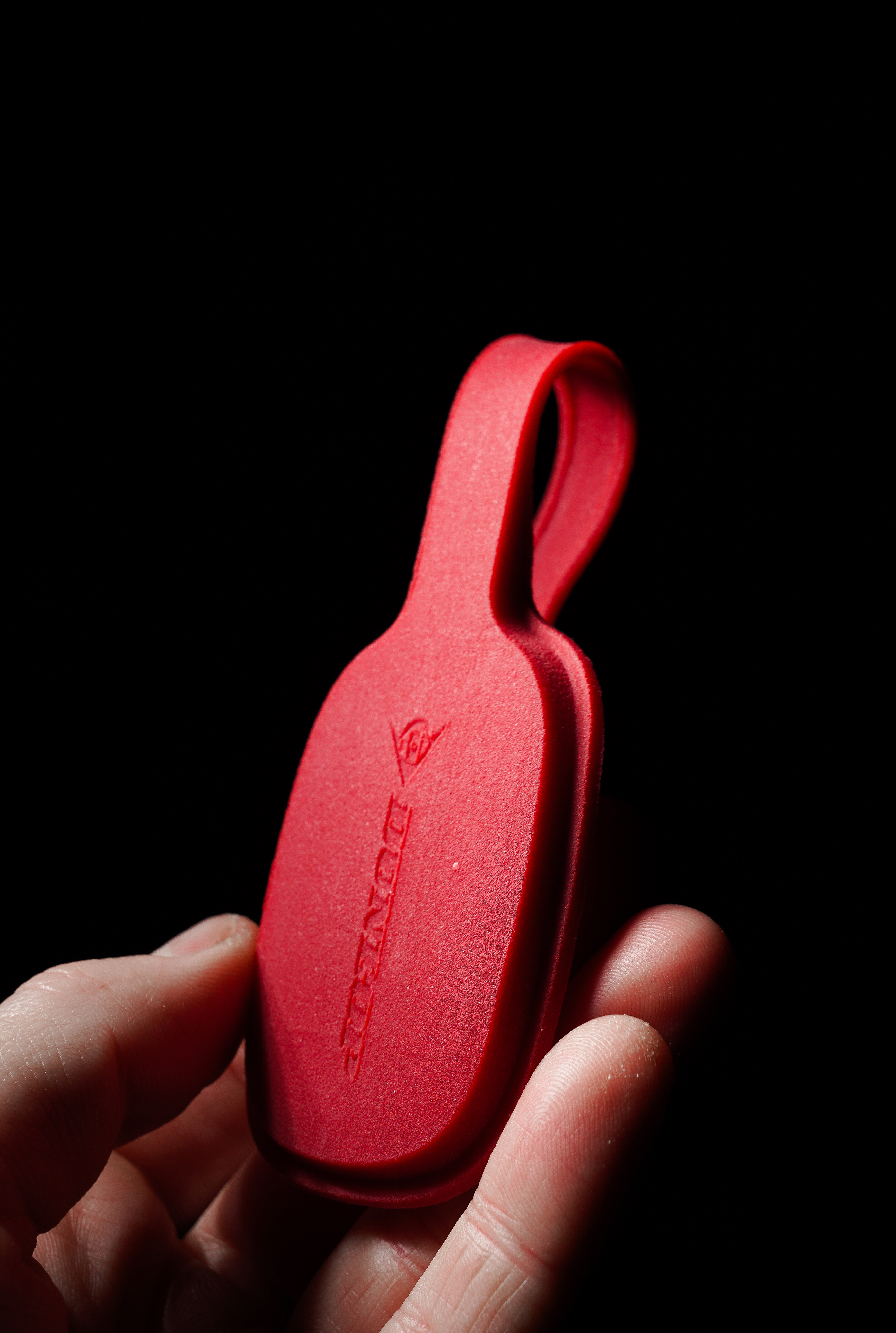
Modular, flexible, PCB aesthetic.
Every aspect designed to enhance the
insert's experience, usability, and functionality was intentionally communicated
through its design. Flexibility, pressure
sensing, modularity, malleability, and an aesthetic reminiscent of
a printed circuit board, ensuring a cohesive and intuitive user experience.

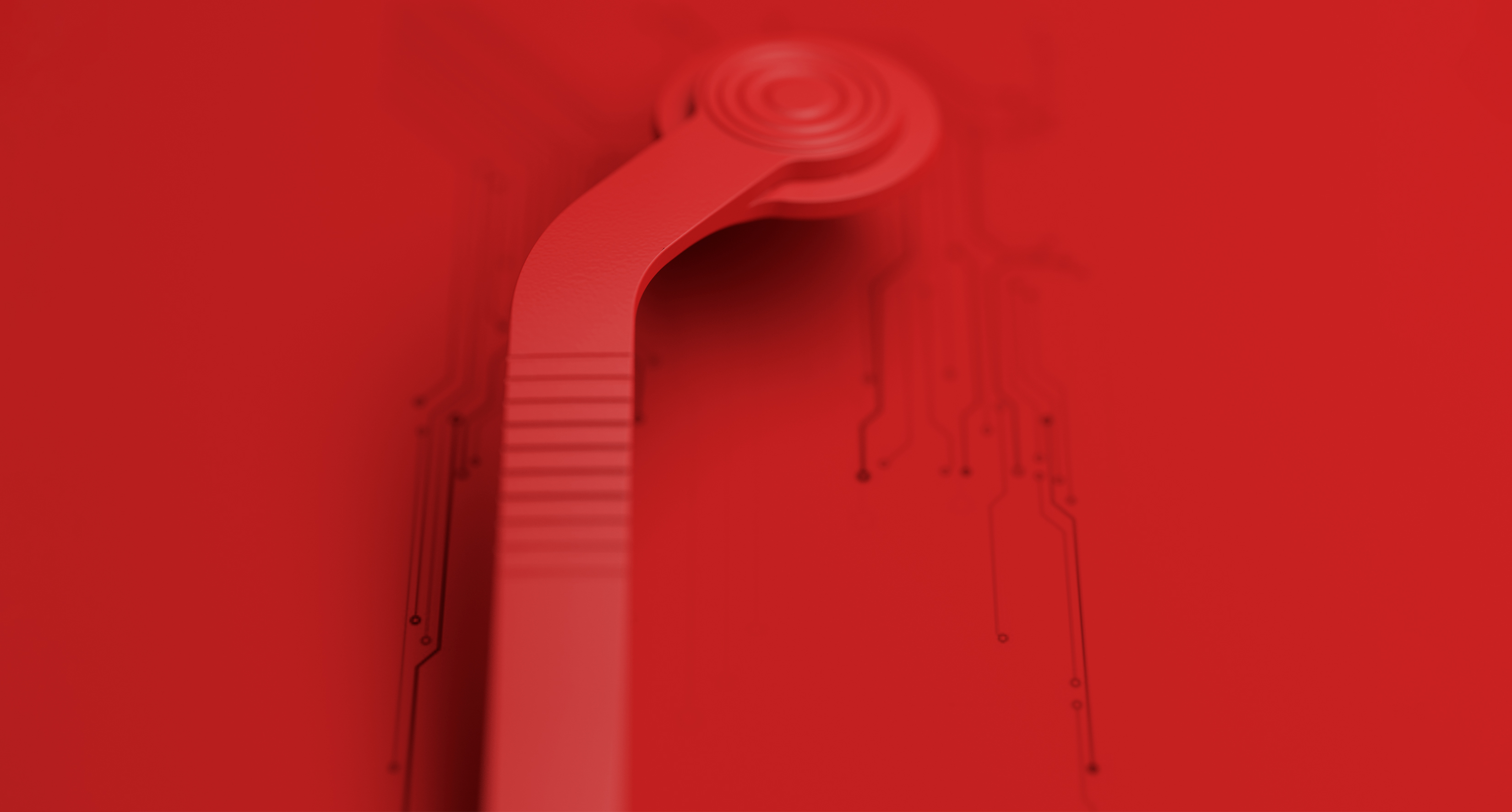



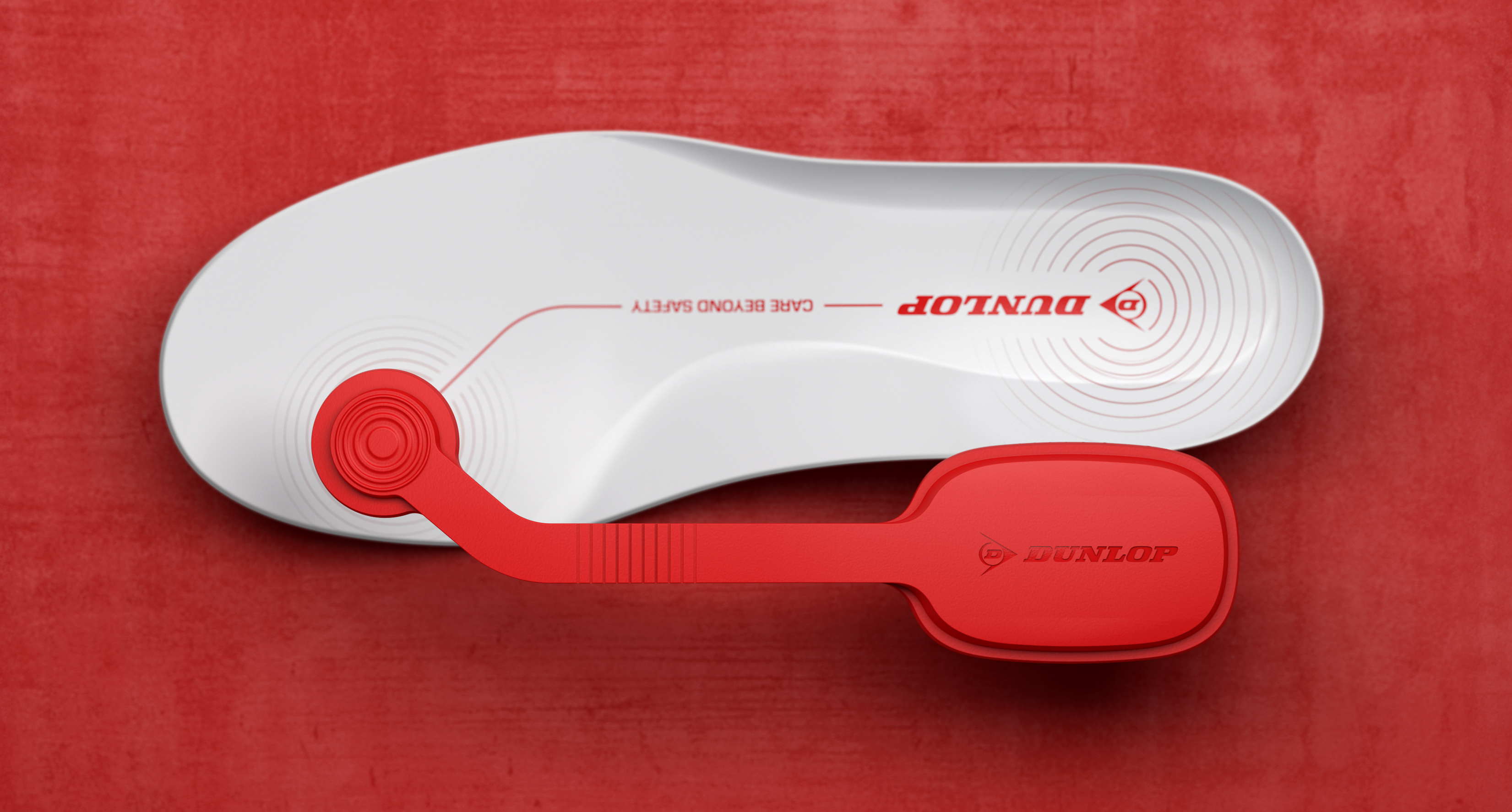
Further robust performance testing.
Dunlop
has collaborated with various companies to conduct initial testing on the first
prototypes of the SmartInsole. Aiming to assess
the performance, durability, and user experience in real-world scenarios.
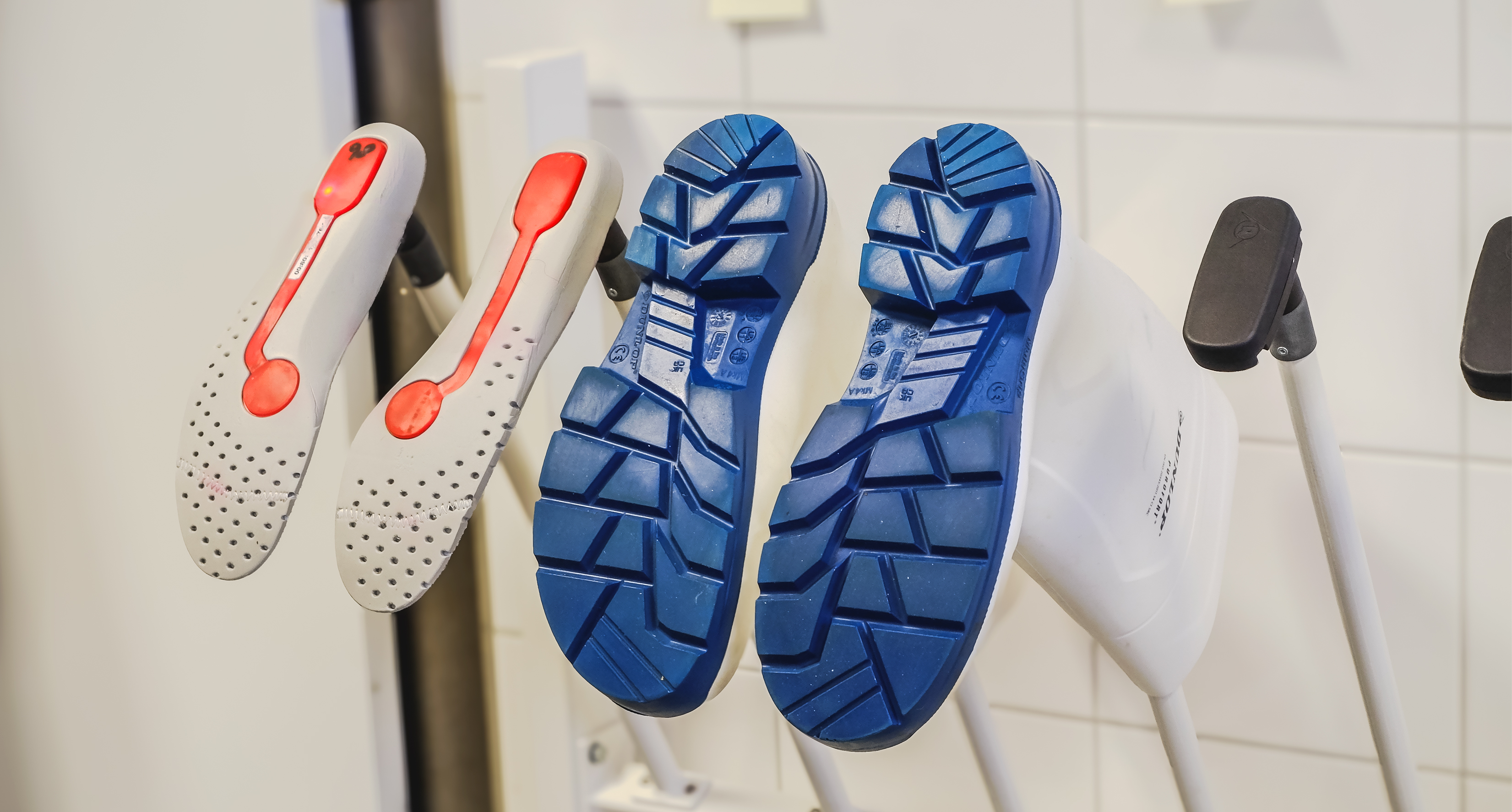
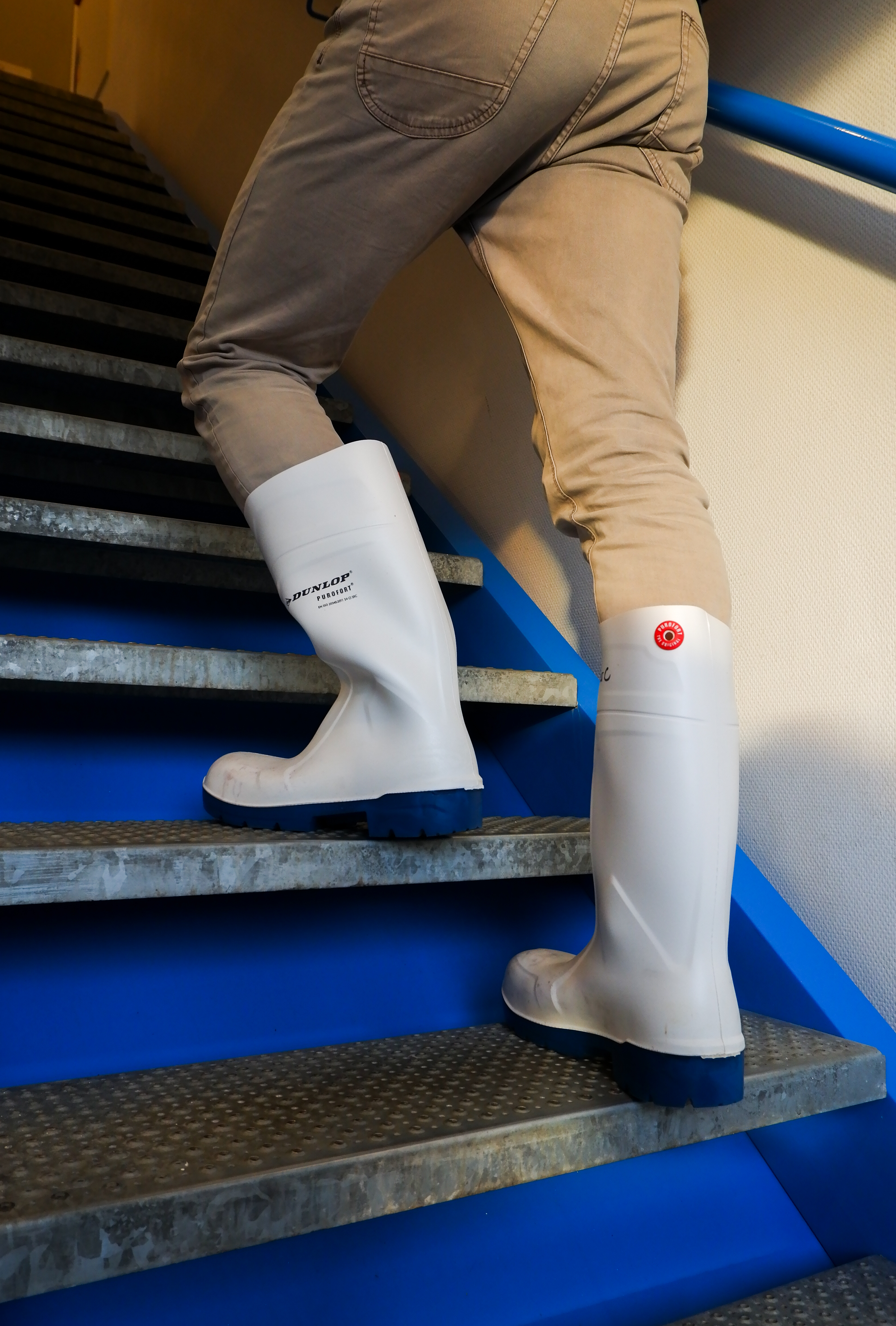
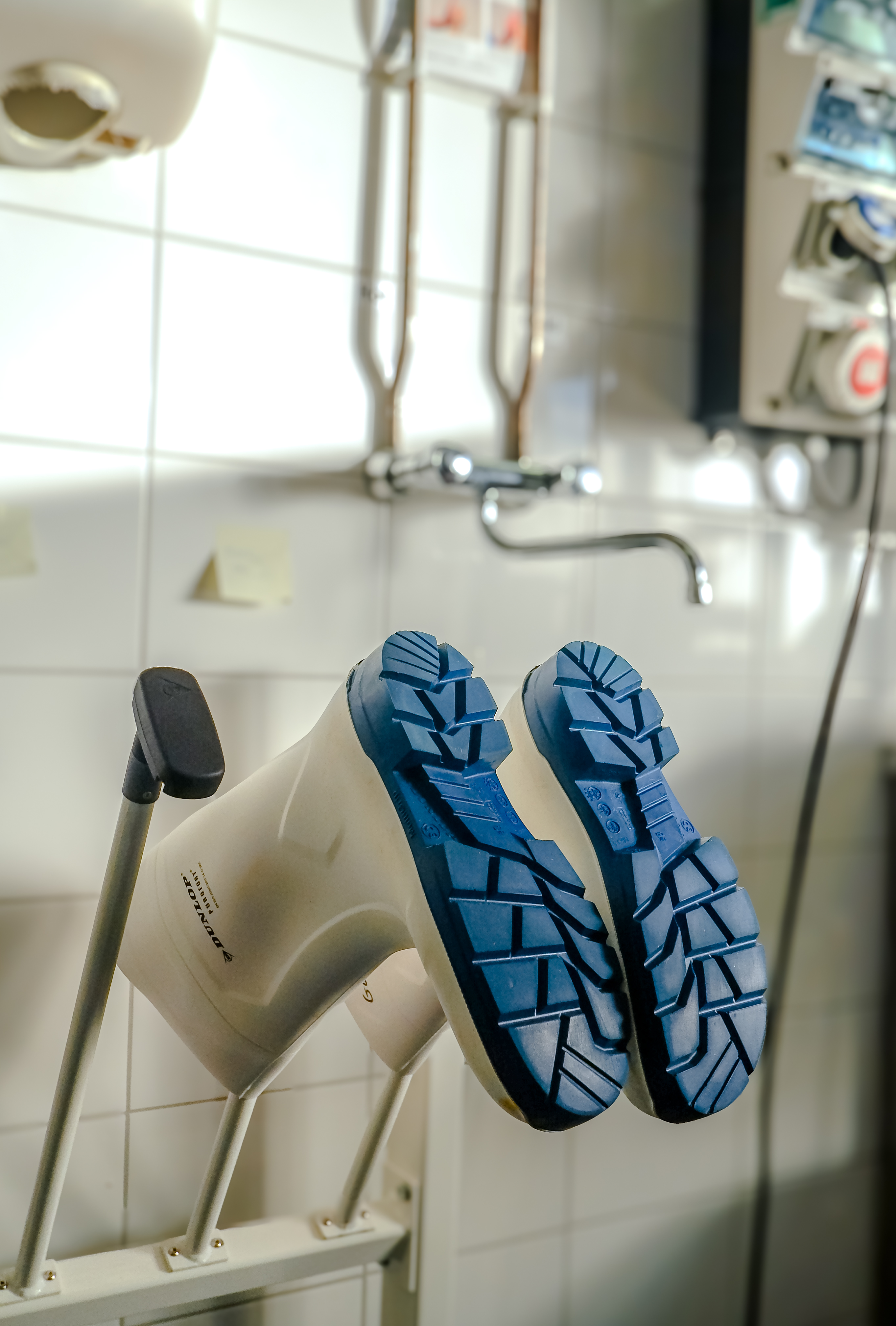
Learn, implement, and develop.
Leveraging
the insights and learnings gained from these tests, Dunlop is actively
utilising the feedback to enhance the overall performance. Incorporating user feedback and addressing any identified challenges, ensuring
a truly innovative and impactful solution is brought to market later down the line.
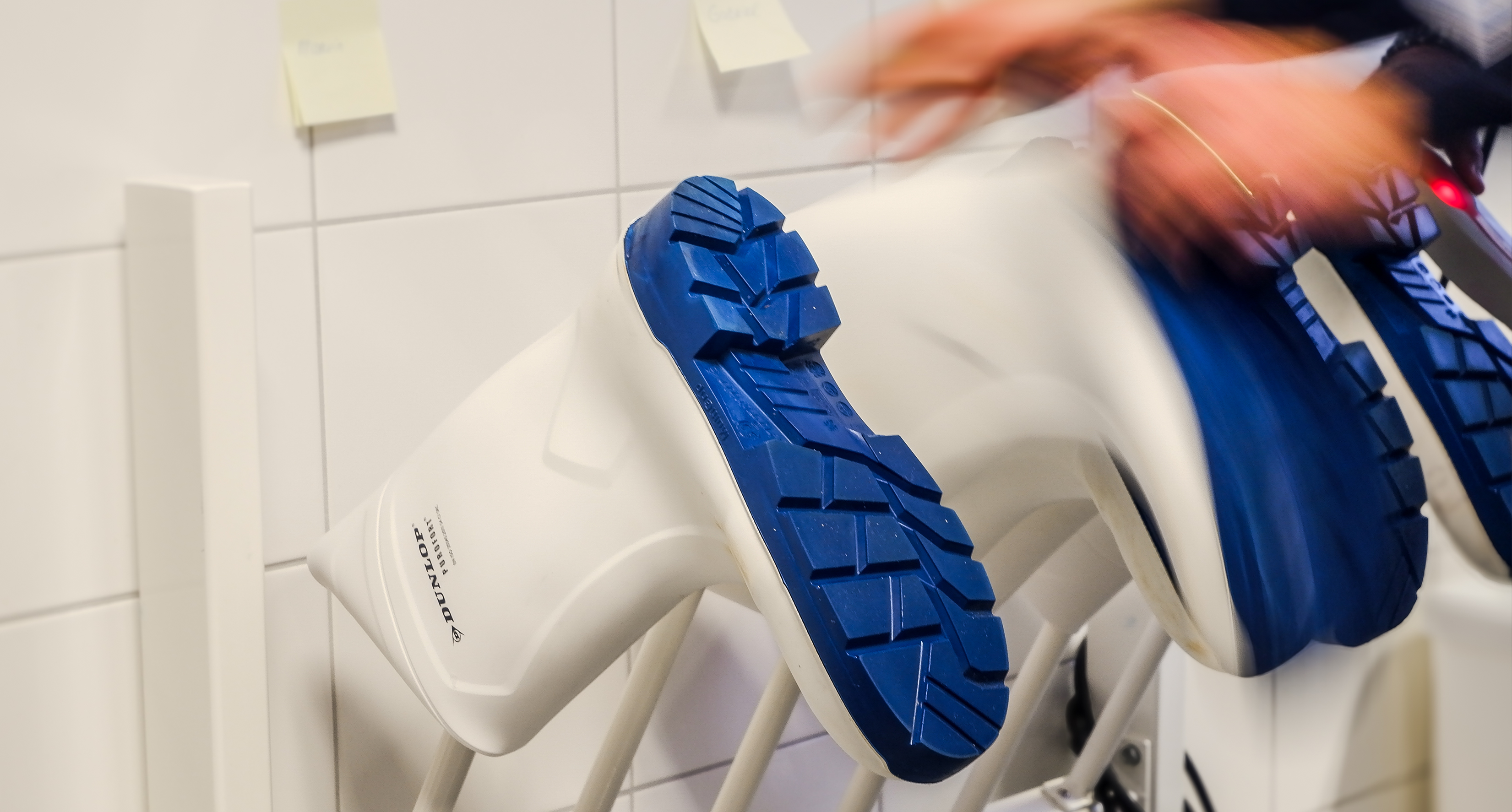